A company I know of in Wisconsin recently stopped using Creo and opted instead to migrate their entire company to Inventor. If you know me you know I can be quite opinionated and I've heard it all. My favorite is 'Bart, you don't understand. Our vendors use Solidworks". "We should be using solidworks" So where am i going with this? Let me try to explain the difference between a vendor and a a partner I will also try to explain the difference between a mid range modeler such as solidworks, Inventor and a high end modeler such as Catia, Creo and NX.
When did the progressive manufactures quit empowering their vendors to take full leverage of the tools we now call Creo?
Lets take for example that you have Creo and your a fortune 500 company. Maybe you group or team does not own all the various modules but if you mature to the point that you realize you need Creo Simulate or Creo Style or Sheetmetal's Progressive Die extension or any other module that when you first purchased Creo you didn't know you need, at least there exists a module you can purchase but did not when you made your initial investment. With Solidworks, Inventor and the like your only get what you get. These mid range tools mentioned are a one module systems. There is no other module that you can purse if you had the desire. You simply made a mistake or you wait for the developer to write in the code for more functionality.
This happened to Tesla. They purchased their seats of Solidworks and later figured out they needed more. (smart people are smart because they know they don't know everything) When Tesla matured they realized they needed more out of Solidworks than the two module system that it came with. Like G2 and G3 continuity among about 600 other things that Creo and Catia can do with their hundreds of modules. The same sales person who sold them Solidworks sold them Catia. They should have purchased Catia instead. Or Creo!
In my classes I like to explain the difference between a vendor and a partner. You tell vendors what to do not how to do it. A partner you invite to training with you. Not to many companies think to invite their design firms for training. Even as it's a day rate it doesn't cost more. Caterpillar purchased Pro/ENGINEER for select vendors converting them into partners in the late 80's. The ones that refused to quit using AutoCAD went out of business quickly as Caterpillar trained the one vendor to be a partner. Trained them to use Pro/ENGINEER and many went for 30k per month of business to 230k per month in business.
Converting from Creo to Solidworks or Inventor both tools are a 'one module system' is one step short of going out of business.
Saturday, April 16, 2016
Vender or Partner: What is the difference?
Monday, April 11, 2016
Creo 3.0 has a new render engine and we like it. These are screen grabs and not even renderings. Using Mental Ray these images were created inside of Creo 3.0 Not all the tools of mental ray are exposed but it's a great start. Maybe in future releases we can get decent renders with out exporting to Maxwell or Keyshot. visit design engine website now http://www.proetools.com
Friday, January 04, 2013
Metric: What is the value for training?
I often get managers who don't often believe in training or possibly they don't have a budget for training. It dawns on me that there is no metric so to offer to convince training is necessary. So I put together this Blogger entry to help managers understand value in training. It seems to me that the SolidWorks companies are the hardest to convince that training is necessary. Who does a metric anyway? Is it of value to make a 2% improvement? Just 2% on a race track is a huge number. What if we could get your engineering staff a 15% improvement over the last project?
WHY:
Engineers are natural problem solvers. They figure out how things work and design products out of innate skill through intelligence, discovery, innovation and grit. A typical engineer can learn a great deal in a week as they go through their week and develop or enhance new products. They often ‘figure it out on the job’. as it is often stated. After all, that’s why one would hire an engineer in the first place, to figure things out. That is where Design-Engine can step in (or be utilized). Design-Engine can offer modeling techniques and specific training to aid in an engineer’s ability to solve problems using SolidWorks. Often times, times savings are just 5 to 15 percent added efficiency. Other times it’s a $40,000 savings in tooling, but every time it’s added confidence. There is no metric for this money and time savings, and thus this can go un-noticed.
People also tend to be set in their ways when it comes to design and engineering. Engineers often do the same things each time to obtain their designs. People also tend to have preconceived notions when it comes to design & amp; design habits. Through Design-Engine instructor lead example training, one can open up the designer/engineer mind to alternate and often more mature modeling technique. Many techniques for managing design changes are often dismissed such as with the top down modeling methodology.
People come from many backgrounds and pool experiences from their various work history. They have used SolidWorks for years but often misinterpreted or misunderstood SolidWorks basics. http://proetools.com/solidworks-training-level-1-introduction-to-constraint-based-modeling/ Before taking a training class the very definition of ‘the basics’ is often different from participants after an instructor lead Design-Engine training course. For example, I thought I was a surfacing expert in the mid 90's and a decade later I realized how little I knew back then.
WHAT:
1 Design-Engine instructors will offer specific workflow and/or change techniques for managing design changes to models and designs.
2 Share top down modeling methodologies for managing significant changes to form, projects and products.
3 Utilize drawing tools for managing design changes as opposed to documentation.
Demystify specific features (to name a few)
1 Sweeps, Rails, Surface Loft and Surface Boundary functions. That's our Solidworks Surfacing class http://proetools.com/solidworks-surfacing-intensive/
2 Utilizes more robust curves + Surfaces to accomplish normal tasks more efficiently.
3 Work more efficiently with 2D and 3D IGES geometry.
4 Learn animation and motion analysis creating effective animations for your manager to communicate more effectively to sales and marketing.
Offer a fresh look at common tools
1 Use sketch curve geometry to manage tubular frame structures. Everyone knows how to use sketch and curve geometry. Applying it for specific tasks may be new. We call incorporating every day tools to preform different tasks, "incorporating into your workflow".
2 Discuss robust modeling techniques by leveraging parent/child relationships. People moving from Rhino or Alias have not yet discovered how to leverage parent/child relationships nor have they embraced the parametric workflow. A fresh look at a these functions can be most exciting.
3 Utilize equations for minimizing mistakes. Our training is example based, so simply making a statement like this has no meaning until examples are presented. Then participants often realize where they themselves could have benefited from this added to ones workflow.
4 Use Sheetmetal functions more effectively. Or consider our Solidworks Sheetmetal class http://proetools.com/solidworks-sheetmetal-solidworks-training/
There is a lot of valuable information there on our various Solid Works classes, on the following website links:
http://proetools.com/category/courses/solidworks/
Companies seldom offer their engineers SolidWorks update training. Design-Engine can offer update training to cover years of updates in several hours or several days. Depending upon the budget and if the presentation is lecture oriented or participants get to try the examples. New functions get added to the software with each release and your staff may not leverage those enhancements into their everyday workflow. Our heavy user training can touch on these enhancements.
Conclusion
Companies believe in empowering their staff through new ideas but update training or SolidWorks training may be categorized differently. It is an option to let engineers fend for themselves. Through our instructor led example oriented training efforts, Design-Engine in it’s training effort aims to aid engineers in thinking differently, smarter and more efficiently. Expect the participants to be more adept, efficient, confident, to making accurate time estimates. In essence we free up design staff to work smarter not harder.
Thank you for taking the time to read
WHY:
Engineers are natural problem solvers. They figure out how things work and design products out of innate skill through intelligence, discovery, innovation and grit. A typical engineer can learn a great deal in a week as they go through their week and develop or enhance new products. They often ‘figure it out on the job’. as it is often stated. After all, that’s why one would hire an engineer in the first place, to figure things out. That is where Design-Engine can step in (or be utilized). Design-Engine can offer modeling techniques and specific training to aid in an engineer’s ability to solve problems using SolidWorks. Often times, times savings are just 5 to 15 percent added efficiency. Other times it’s a $40,000 savings in tooling, but every time it’s added confidence. There is no metric for this money and time savings, and thus this can go un-noticed.
People also tend to be set in their ways when it comes to design and engineering. Engineers often do the same things each time to obtain their designs. People also tend to have preconceived notions when it comes to design & amp; design habits. Through Design-Engine instructor lead example training, one can open up the designer/engineer mind to alternate and often more mature modeling technique. Many techniques for managing design changes are often dismissed such as with the top down modeling methodology.
People come from many backgrounds and pool experiences from their various work history. They have used SolidWorks for years but often misinterpreted or misunderstood SolidWorks basics. http://proetools.com/solidworks-training-level-1-introduction-to-constraint-based-modeling/ Before taking a training class the very definition of ‘the basics’ is often different from participants after an instructor lead Design-Engine training course. For example, I thought I was a surfacing expert in the mid 90's and a decade later I realized how little I knew back then.
WHAT:
1 Design-Engine instructors will offer specific workflow and/or change techniques for managing design changes to models and designs.
2 Share top down modeling methodologies for managing significant changes to form, projects and products.
3 Utilize drawing tools for managing design changes as opposed to documentation.
Demystify specific features (to name a few)
1 Sweeps, Rails, Surface Loft and Surface Boundary functions. That's our Solidworks Surfacing class http://proetools.com/solidworks-surfacing-intensive/
2 Utilizes more robust curves + Surfaces to accomplish normal tasks more efficiently.
3 Work more efficiently with 2D and 3D IGES geometry.
4 Learn animation and motion analysis creating effective animations for your manager to communicate more effectively to sales and marketing.
Offer a fresh look at common tools
1 Use sketch curve geometry to manage tubular frame structures. Everyone knows how to use sketch and curve geometry. Applying it for specific tasks may be new. We call incorporating every day tools to preform different tasks, "incorporating into your workflow".
2 Discuss robust modeling techniques by leveraging parent/child relationships. People moving from Rhino or Alias have not yet discovered how to leverage parent/child relationships nor have they embraced the parametric workflow. A fresh look at a these functions can be most exciting.
3 Utilize equations for minimizing mistakes. Our training is example based, so simply making a statement like this has no meaning until examples are presented. Then participants often realize where they themselves could have benefited from this added to ones workflow.
4 Use Sheetmetal functions more effectively. Or consider our Solidworks Sheetmetal class http://proetools.com/solidworks-sheetmetal-solidworks-training/
There is a lot of valuable information there on our various Solid Works classes, on the following website links:
http://proetools.com/category/courses/solidworks/
Conclusion
Companies believe in empowering their staff through new ideas but update training or SolidWorks training may be categorized differently. It is an option to let engineers fend for themselves. Through our instructor led example oriented training efforts, Design-Engine in it’s training effort aims to aid engineers in thinking differently, smarter and more efficiently. Expect the participants to be more adept, efficient, confident, to making accurate time estimates. In essence we free up design staff to work smarter not harder.
Thank you for taking the time to read
Wednesday, July 04, 2012
From a motorcycle racers perspective. "Whats your Favorite Race Track?"
I was asked the other day what my favorite track was and why? There needs to be a metric for determining what makes a track good bad or ugly. In the seventh grade we as North Americans at least learn to categorize things. There are so many categories for reasons to like or dislike a race track.
One would almost have to create a points rating or a metric for
categorizing tracks and after thinking about it I could not stop thinking about it. Ive been racing sportbikes for two years now and have built time on 20 +
tracks so my attempt to make a rating system starts by listing pros and
cons of each track all from a motorcycle perspective of course. Ill leave out tracks that have banking like Iowa
speedway, Indy, Knoxville Speedway and Daytona. I have videos of most
of these tracks listed below on youtube http://www.youtube.com/user/bbrejcha
Like or like to hate? Most people I've met would love to be on any track no matter. Maybe you can add to this list at the bottom? What are your thoughts for a Metric? What track to you despise?
http://www.autobahncc.com/
AutoBahn (Joliet) is a favorite track and comes with two track options a north and a south course. It's the closest track to me in Chicago and I have friends that are members there. There is even a connector making a 27 turn course. (I have videos on youtube of the full course) North Course by itself is sketchy at T1 and should be taken at 80 percent. it is possible North course T3 could offer more run off and less guard railing. In the wet there is often standing water and they do have a drainage problem. The blend line is idiotic for both north And South course and the track designer should be embarrassed and ridiculed. They should spend some money and add pavement for a new way to enter both courses. South Course is flowing and technical. Many complain about the acceleration whoops form the cars hard acceleration in T6 but I like the bumps personally. I think those bumps makes the track more interesting. T3 and T13 and T14 could use more room for crashing and less guard rail. For those reasons Autobahn can't make the top three.
http://www.barbermotorsports.com
Barber needs to be scaled up in AutoCAD 30 percent. I love Barber despite that! It's probably the most expensive track to rent for track day organizations. Is that true? Its got great traction in the rain but there are some standing water spots even rivers crossing the track in the rain. You will hydroplane each lap to win in the rain. Get used to that if you want to go fast in the rain at Barber. T1 could use some more run off maybe? Museum and paddock make Barber A Class! Barber the race track makes one forget that Martin Luther King was shot and killed in Birmingham. Maybe I should not have mentioned that?
http://www.blackhawkfarms.com/
Blackhawk Farms Beloit IL is narrow, deadly dangerous in their T2, T4, T5 (Trees) with zero traction in the wet due to all the Mazda Miata's that turn upside down there probably even the weekend before your there. They can't move the trees because the acreage is protected by some wetland bull sh*t. It's sad and probably an excuse. If it were my land I would poison the trees that I wanted to remove and after they die yank them the hell out. Many people are learning to walk again due to T2 there. The Helicopter comes fast and that's good I guess. It's technical and challenging which is great! Takes a butt load of laps to figure that track out proving to everyone it's hard and a challenge to learn. The track management is cool tho and they try very hard to please the motorcycle folks. They recently spent some money on a new building and did some much needed repairs to the track.
http://www.grattanraceway.com/
Grattan in Grattan MI The road Course there is like a motocross track scaled up and paved. And freshly paved at that. Technical and flowing as well. Is there an ugly place to crash? Could use some sand in run off places I guess.... High marks for Grattan. It even has some interesting blind spots which is a plus in my book. Grattan can be run and raced backwards which gives it even more high marks. Oh Crap. I forgot to mention they have a motocross track and a swimming pool there too! I dont have as much time at Grattan as I would like since this track has to be the top of my list.
http://www.jenningsgp.com/
Jennings GP Jennings FL -Darn cool track. It's technical and flowing with killer traction in the wet because the filler is washed out from the aggregate which leaves little rocks sticking up for plenty of room for water to escape. Since there are no cars on that track there is little or no oil from the upside down cars spillage. You can go fast there by only using brakes two times per lap. Jennings can be a bit sandy (but consistent sand) due to the location and sand and there is no elevation changes. Jennings needs a MX track to go with their Motard Addition. I understand they don't do Motard there any longer tho. Sad!

http://www.hpt.com/
Topeka's Heartland Park Raceway is an awesome track especially since they made improvements for the last AMA race that went there. Fast technical and flowing track. Great in the wet little or no places for standing water. Plenty of run off everyplace. T1 takes some balls at an expert race pace.
http://www.midohio.com/
Mid Ohio has some really cool rolling hills. Not a great place to crash in that T1. Great Facility with the paddock and emergency crews.
http://putnampark.com
Putnam Putnam is a technical fast flowing track with plenty of room for passing. Good to Great traction in the wet. Not too much for standing water either. The only real problem with Putnam is that last turn. Loosing the front there you may put you in need a helicopter and poop in a bag for life. 85 percent there for sure. no camping at Putnam and hotels can be on short demand. I've camped in the hotel parking lot before... Don't forget to join the hotel guests for your continental breakfast after camping in a hotel parking lot! That last turn dilemma and subsequent wall .... for that reason alone Putnam can't make my top three.
http://www.roeblingroad.com/
Robeling Road Savanna GA - T1 could use more runoff and it's a bit too flowing everyplace else making it not as technical as one might want to make for better places to overtake. The track managers are "Red Neck Ugly People" which reminds me of the love scene in the movie Deliverance.
http://www.roadamerica.com/
Elkart Lake's Road America could use a bit more crash room in T1 and Canada Corner (remove one mountain and place it at T1) Problem with crashing @ Road America is it's set up for Cars (like many tracks). If you crash in T7 for example there is a 3 to 4" step up from Grass to Rocks and that can damage a spine. Traction in the wet on the paved patches sections 'sux arse' in T5, T6, T8. I crashed in the wet on my sighting lap in practice in the wet there in May and I was just putting around. The long strait's are a little boring and offer in my opinion too much time to rest and for tires to cool. Maybe that's good? Emergency Crew at Road America is top notch!
http://www.roadatlanta.com/
Road Atlanta Braselton, GA- Top ratings for Road Atlanta from me. I was there racing motocross in 1979 as a kid and have great early memories. It offers multiple configurations and with new T12 it's not so deadly. Plenty of room to crash everywhere. Maybe flipping off at T5 you could hit something. I grew up 30 minutes from this track in Lilburn / Stone Mountain GA
I list my favorites this way
1 Grattan I wish CCS raced at Grattan. Ill try to be there for the WERA weekend July 2012!
2 Road Atlanta
3 Barber
What's your favorite track? Post below.
Like or like to hate? Most people I've met would love to be on any track no matter. Maybe you can add to this list at the bottom? What are your thoughts for a Metric? What track to you despise?
http://www.autobahncc.com/
AutoBahn (Joliet) is a favorite track and comes with two track options a north and a south course. It's the closest track to me in Chicago and I have friends that are members there. There is even a connector making a 27 turn course. (I have videos on youtube of the full course) North Course by itself is sketchy at T1 and should be taken at 80 percent. it is possible North course T3 could offer more run off and less guard railing. In the wet there is often standing water and they do have a drainage problem. The blend line is idiotic for both north And South course and the track designer should be embarrassed and ridiculed. They should spend some money and add pavement for a new way to enter both courses. South Course is flowing and technical. Many complain about the acceleration whoops form the cars hard acceleration in T6 but I like the bumps personally. I think those bumps makes the track more interesting. T3 and T13 and T14 could use more room for crashing and less guard rail. For those reasons Autobahn can't make the top three.
http://www.barbermotorsports.com
Barber needs to be scaled up in AutoCAD 30 percent. I love Barber despite that! It's probably the most expensive track to rent for track day organizations. Is that true? Its got great traction in the rain but there are some standing water spots even rivers crossing the track in the rain. You will hydroplane each lap to win in the rain. Get used to that if you want to go fast in the rain at Barber. T1 could use some more run off maybe? Museum and paddock make Barber A Class! Barber the race track makes one forget that Martin Luther King was shot and killed in Birmingham. Maybe I should not have mentioned that?
http://www.blackhawkfarms.com/
Blackhawk Farms Beloit IL is narrow, deadly dangerous in their T2, T4, T5 (Trees) with zero traction in the wet due to all the Mazda Miata's that turn upside down there probably even the weekend before your there. They can't move the trees because the acreage is protected by some wetland bull sh*t. It's sad and probably an excuse. If it were my land I would poison the trees that I wanted to remove and after they die yank them the hell out. Many people are learning to walk again due to T2 there. The Helicopter comes fast and that's good I guess. It's technical and challenging which is great! Takes a butt load of laps to figure that track out proving to everyone it's hard and a challenge to learn. The track management is cool tho and they try very hard to please the motorcycle folks. They recently spent some money on a new building and did some much needed repairs to the track.
http://www.grattanraceway.com/
Grattan in Grattan MI The road Course there is like a motocross track scaled up and paved. And freshly paved at that. Technical and flowing as well. Is there an ugly place to crash? Could use some sand in run off places I guess.... High marks for Grattan. It even has some interesting blind spots which is a plus in my book. Grattan can be run and raced backwards which gives it even more high marks. Oh Crap. I forgot to mention they have a motocross track and a swimming pool there too! I dont have as much time at Grattan as I would like since this track has to be the top of my list.
http://www.jenningsgp.com/
Jennings GP Jennings FL -Darn cool track. It's technical and flowing with killer traction in the wet because the filler is washed out from the aggregate which leaves little rocks sticking up for plenty of room for water to escape. Since there are no cars on that track there is little or no oil from the upside down cars spillage. You can go fast there by only using brakes two times per lap. Jennings can be a bit sandy (but consistent sand) due to the location and sand and there is no elevation changes. Jennings needs a MX track to go with their Motard Addition. I understand they don't do Motard there any longer tho. Sad!

http://www.hpt.com/
Topeka's Heartland Park Raceway is an awesome track especially since they made improvements for the last AMA race that went there. Fast technical and flowing track. Great in the wet little or no places for standing water. Plenty of run off everyplace. T1 takes some balls at an expert race pace.
http://www.midohio.com/
Mid Ohio has some really cool rolling hills. Not a great place to crash in that T1. Great Facility with the paddock and emergency crews.
http://putnampark.com
Putnam Putnam is a technical fast flowing track with plenty of room for passing. Good to Great traction in the wet. Not too much for standing water either. The only real problem with Putnam is that last turn. Loosing the front there you may put you in need a helicopter and poop in a bag for life. 85 percent there for sure. no camping at Putnam and hotels can be on short demand. I've camped in the hotel parking lot before... Don't forget to join the hotel guests for your continental breakfast after camping in a hotel parking lot! That last turn dilemma and subsequent wall .... for that reason alone Putnam can't make my top three.
http://www.roeblingroad.com/
Robeling Road Savanna GA - T1 could use more runoff and it's a bit too flowing everyplace else making it not as technical as one might want to make for better places to overtake. The track managers are "Red Neck Ugly People" which reminds me of the love scene in the movie Deliverance.
http://www.roadamerica.com/
Elkart Lake's Road America could use a bit more crash room in T1 and Canada Corner (remove one mountain and place it at T1) Problem with crashing @ Road America is it's set up for Cars (like many tracks). If you crash in T7 for example there is a 3 to 4" step up from Grass to Rocks and that can damage a spine. Traction in the wet on the paved patches sections 'sux arse' in T5, T6, T8. I crashed in the wet on my sighting lap in practice in the wet there in May and I was just putting around. The long strait's are a little boring and offer in my opinion too much time to rest and for tires to cool. Maybe that's good? Emergency Crew at Road America is top notch!
http://www.roadatlanta.com/
Road Atlanta Braselton, GA- Top ratings for Road Atlanta from me. I was there racing motocross in 1979 as a kid and have great early memories. It offers multiple configurations and with new T12 it's not so deadly. Plenty of room to crash everywhere. Maybe flipping off at T5 you could hit something. I grew up 30 minutes from this track in Lilburn / Stone Mountain GA
I list my favorites this way
1 Grattan I wish CCS raced at Grattan. Ill try to be there for the WERA weekend July 2012!
2 Road Atlanta
3 Barber
What's your favorite track? Post below.
Monday, April 30, 2012
'The new Design Engine logo' Vinyl Graphics GSXR 600
Design Engine has updated it's logo in order to bring the several design engine sites together. There is the jobs forum. http://jobs.designengine.com then the design engineering blog http://www.designengine.com then the school itself http://www.proetools.com Notice the new logo on each of those pages.
One of the cool things of working at Design Engine is how much each gets to learn. From Social marketing to brain storming to vinyl wraps. Everything in an engineer or designers life is about learning anyway and we just find ourselves constantly learning. Whether it's swimming at a better pace, steady more controlled moves in yoga or smoother faster lines on the race track it's always about how fast can you reason through problems and ultimately how fast one can learn. That is what we are about at Design engine learning (as we teach designers how to learn new software) and in this project we set out to learn how to design and apply vinyl graphics so that possibly next fall we can administer a course utilizing all we have learned. Illustrator, design iteration process, vinyl wrap combination. Back to the new logo....
To kick off the new logo we showed it off first on the design-engine Suzuki GSXR600 race bike which is competing in 600 Middleweight, Supersport, GTU, Heavyweight, Superbike and GP Midwest Expert races in the Champion Cup Series CCS expert series for 2012. The images tell the story.
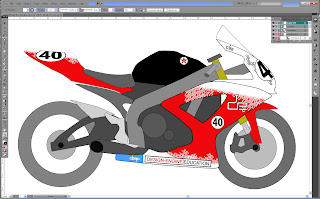
the Adobe Illustrator line art 2012 design 'looks like model'
We started the vinyl wrap project by looking at race bikes from current and
previous years. A little internet 'see whats out there' research never hurt anyone. We liked nothing we saw out there and we wanted to do
something unique yet utilize a design that would leverage the
illustrator/vinyl strengths. In our research we noticed people were doing a sort of different tribal looks with vinyl applications like Huntly Nash's #75 race bike graphics from last year http://www.huntleynash.com/ and the Michael Jordan Race Team bikes that have been wrapped over the years. http://www.23race.com/ or the AMA Safety First Police Race bikes of 2005 - 2008. All very busy graphically. We wanted to explore the use of vinyl graphics without getting too much graphically. Hope you enjoy a glimpse into our world from this picture log.
applying vinyl to the upper faring
The Vinyl we used is a 3mil cast vinyl. It is stretchy stuff. We used a Kawasaki heat Gun to heat up the more compound areas and we were especially careful not to stretch and distort the vinyl where graphics are concerned.
Max with the printed artwork
Max is pictured with the printed Adobe Illustrator vector art all all ready
for application to the race plastic. Yes we made a mess but nothing the super-dope Rainbow Vacuum Cleaner can't handle (that product's latest iteration
was designed developed using Pro/E and copied by Dyson by the way) And yes, we work in trade sometimes.
the rear cow completed (white number plates for expert)
Notice the white bleed out to Red and the round number plates. We wanted to showcase the new logo coming out of the white portion , something one can't easily do with paint. The finished product has white on top and bottom and a red in the middle sections. We thought the round number place stands out this way.
'Template File' (what we send to print)
Typically a printer will want an Adobe Illustrator file PDF complete with layers. One layer for the color graphics and another layer for a magenta die cut line.
using masking tape to obtain the flat for the compound surfaces
One challenge with vinyl graphics is simply applying the vinyl without the vinyl sticking to itself. Another challenge is getting the air pockets out properly. Yet another challenge is understanding what flat pattern to utilize from compound surfaces such as found on motorcycle race plastic, not to mention applying those graphics to the farings. We used a hot glue gun to help the vinyl stick on the b-side of the faring surfaces.
A spot of bother as they say in England
If you are interested in one of the Design Engine Illustrator workshops consider taking our one or two week Adobe Illustrator intensive to learn the basics of Illustrator, develop graphics for your project then learn how to apply your printed vinyl graphics. We intend for the class to occur in the Fall of 2012 and will probably utilize several instructors. The curriculum is not set nor has been set but do send in your inquiry so we can use your input to plan the course dates and structure. http://proetools.com/category/courses/adobe/
Whats next? We are still busy with Vinyl Graphics this year! Design Engine has two Yamaha Zuma Scooters for it's employees and out of town students to enjoy. You guessed it, they are being wrapped too. Oh and the Design Engine YZ450's too.
The completed race bike at Heartland Park Raceway in Topeka KS
The completed graphics T4 Blackhawk Farms Raceway BFR
Special thanks to Max who is learning the seemingly black art of vinyl wrapping compound surfaces! I know he was joking but when Max said he was going to wrap the coffee maker I cried in laughter. If he doesn't wrap the coffee maker I will!
Wednesday, June 30, 2010
Pro/E vs SolidWorks
At Design Engine tonight we are doing a Pro/E vs Solidworks shootout where Im running solidworks. Except Im known as the Pro/E surfacing expert not the solidworks surfacing expert. In order to accurately evaluate the Modeling software of both Pro/ENGINEER and Solidworks each participant will have a team member in their corner of the ring. http://www.design-engine.com/feature.php?feature=96
I invited several from both Soldworks and PTC however only PTC AE's confirmed.
I pushed the crap out of Solidworks this week to prepare for the shootout so to do some impressive modifications like my one week surfacing students might do in Pro/E. There are a few connections that just fall apart and that frustrates the hell out of me. In SW I expect these connections to work and not like Rhino fall apart. That's frustrating.
Let me explain, that in my experience I have noticed industrial designers want to prove form when developing a product as opposed to simply capture form. I have noticed however many industrial designers are happy to just model a forum (capture form) hence their use of Rhino where they can't leverage strategic advantage of parametric controls nor participate in an intense study of parent child relationships. If we can leverage parent child relationships then we can make 20 modifications in five minutes like we teach ID'ers in my week long Pro/E surfacing intensive. Hence prove the forum in the light reflections.
My techniques for forcing solidworks to swallow twenty slight modifications in rapid fire all in less than four minutes is giving me a problem in a spot or two. Choking on one part and several of my beziar curves will not maintain their parent child relationships. Chris Thompson from Ohio an ME with significant product design experience will be here at three to sit in my corner running Solidworks and will help me through the issues.
My end goal is to make solidworks look great since after such development over the past three years is impressive then share surfacing workflow techniques with the audience. A workflow we at Design Engine are known to teach in our classes. One that I've stated on this forum that some may not have discovered yet.
On the Pro/E side I have two of my past surfacing students both in from Colorado's Karcher Corporation. They are taking a Surface edit workshop. http://www.proetools.com/courses/pro_surface/level8surfaceedit.htm Adam is an industrial designer with two plus years on Pro/E surfacing and in his corner he has Vaughn an engineer with significant product design experience also from Karcher. Vaughn is quite good at surfacing and sits on the surfacing technical committee at PTC on Pro/E. Vaughn is maybe more experienced than Adam who has also taken past surfacing courses. http://www.karcher-usa.com/ Karcher works on some interesting surfacing rotomolded products.
In my corner running Solidworks I have Chris Thomson an ME who is driving from Ohio today. He has significant product design experience using both Pro/E and Solidworks. We both have different modeling techniques and he has not seen the Design Engine workflow for proving form in Wildfire by modifying parts in rapid fire, he has looked at our Pro/E parts and we will have an hour before the event to work out our strategy together.
I invited several from both Soldworks and PTC however only PTC AE's confirmed.
I pushed the crap out of Solidworks this week to prepare for the shootout so to do some impressive modifications like my one week surfacing students might do in Pro/E. There are a few connections that just fall apart and that frustrates the hell out of me. In SW I expect these connections to work and not like Rhino fall apart. That's frustrating.
Let me explain, that in my experience I have noticed industrial designers want to prove form when developing a product as opposed to simply capture form. I have noticed however many industrial designers are happy to just model a forum (capture form) hence their use of Rhino where they can't leverage strategic advantage of parametric controls nor participate in an intense study of parent child relationships. If we can leverage parent child relationships then we can make 20 modifications in five minutes like we teach ID'ers in my week long Pro/E surfacing intensive. Hence prove the forum in the light reflections.
My techniques for forcing solidworks to swallow twenty slight modifications in rapid fire all in less than four minutes is giving me a problem in a spot or two. Choking on one part and several of my beziar curves will not maintain their parent child relationships. Chris Thompson from Ohio an ME with significant product design experience will be here at three to sit in my corner running Solidworks and will help me through the issues.
My end goal is to make solidworks look great since after such development over the past three years is impressive then share surfacing workflow techniques with the audience. A workflow we at Design Engine are known to teach in our classes. One that I've stated on this forum that some may not have discovered yet.
On the Pro/E side I have two of my past surfacing students both in from Colorado's Karcher Corporation. They are taking a Surface edit workshop. http://www.proetools.com/courses/pro_surface/level8surfaceedit.htm Adam is an industrial designer with two plus years on Pro/E surfacing and in his corner he has Vaughn an engineer with significant product design experience also from Karcher. Vaughn is quite good at surfacing and sits on the surfacing technical committee at PTC on Pro/E. Vaughn is maybe more experienced than Adam who has also taken past surfacing courses. http://www.karcher-usa.com/ Karcher works on some interesting surfacing rotomolded products.
In my corner running Solidworks I have Chris Thomson an ME who is driving from Ohio today. He has significant product design experience using both Pro/E and Solidworks. We both have different modeling techniques and he has not seen the Design Engine workflow for proving form in Wildfire by modifying parts in rapid fire, he has looked at our Pro/E parts and we will have an hour before the event to work out our strategy together.
Tuesday, June 08, 2010
Future Pro/E Developmnent
Wildfire 6 (assuming that is what it will be called), scheduled for released in 2011, has a lot planned for higher level surfacing! Since I have an affiliation with technical committee, I am not entirely sure what I can discuss however I can say for me it is the most significant release since ISDX made its debut in 2001. So get your credit cards ready to upgrade your maintenance ;). And I'm not just talking about just the new Sub'D modeling module which is significant in is own right.
One thing of note: there is a significant push for quality. As I heard the PLM lead discuss the four points for excellence, one was Quality. I laughed to my self thinking... "define quality". The speaker went on to define quality. Impressive.
"Quality is a road we are on" he said. He went on to describe quality as user experience, productivity, robustness, power, and exchange. PTC has always in the past focused heavy on power hence it is more powerful than other packages that maintain smaller budgets for development like the mid range modelers. The big push next for PTC Pro/ENGINEER development is in the user experience. He stated that ProE's user interface and experience should be "just plain fun to use". The example for this user experience is in the maturity of tools like welding and harness design tools that are all new in WF5.0. The PLM lead also went on to explain that quality is something you never achieve but something you always strive for. I buy that.
One thing of note: there is a significant push for quality. As I heard the PLM lead discuss the four points for excellence, one was Quality. I laughed to my self thinking... "define quality". The speaker went on to define quality. Impressive.
"Quality is a road we are on" he said. He went on to describe quality as user experience, productivity, robustness, power, and exchange. PTC has always in the past focused heavy on power hence it is more powerful than other packages that maintain smaller budgets for development like the mid range modelers. The big push next for PTC Pro/ENGINEER development is in the user experience. He stated that ProE's user interface and experience should be "just plain fun to use". The example for this user experience is in the maturity of tools like welding and harness design tools that are all new in WF5.0. The PLM lead also went on to explain that quality is something you never achieve but something you always strive for. I buy that.
Labels:
pro/engineer,
proe,
proe training,
PTC
Subscribe to:
Posts (Atom)